Finite Element Analysis
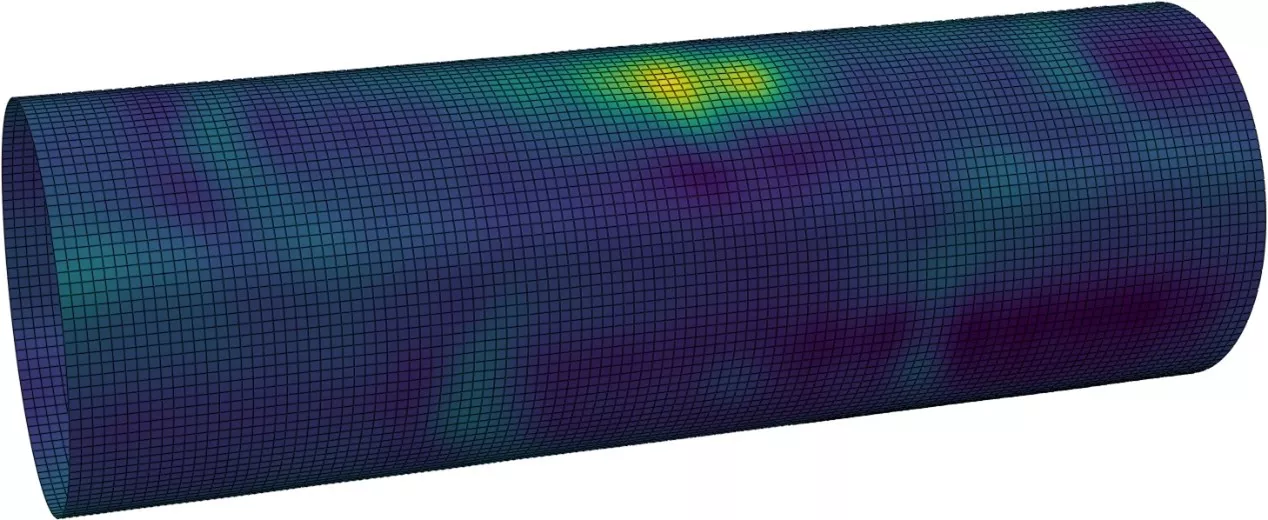
Look Deeper Into Complex Threats
When you are facing the most complex threats, TDW integrity engineers can dive deeper into your pipeline data with Finite Element Analysis (FEA) to provide more advanced assessments and recommendations.
Accurate and Efficient Insights
Not all dents are created equal. When applying API Recommended Practice 1183 for fatigue assessment, those performing Level 3 analysis encounter practical difficulties when it comes to complex dents or large dent populations. But TDW integrity engineers have the experience and advanced in-line inspection (ILI) tools to deliver accurate insights efficiently.
Approach
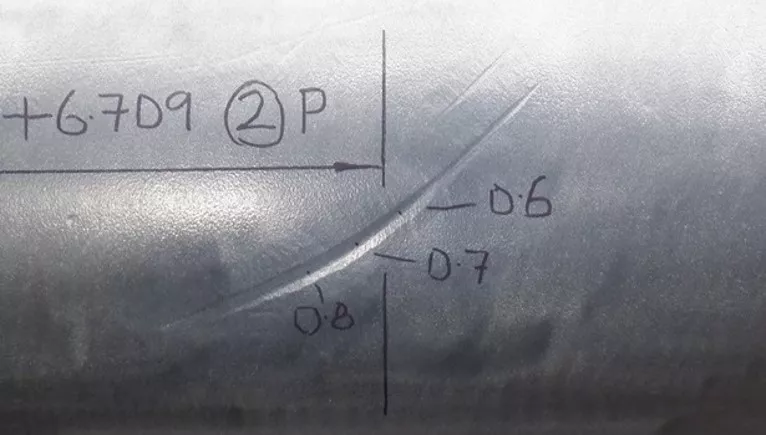
Prepared for Real-World Problems
TDW utilizes FEA methodology based directly on dent shape as measured by ILI:
- Begin with a model geometry using the ILI measured dent shape.
- Apply the internal pressure present at the time of ILI. As the dent re-rounds under internal pressure, the depth will be reduced.
- Compare the predicted dent shape at ILI pressure with the ILI measured shape.
- Adjust the model geometry.
- Iterate steps 2 through 4 until the predicted shape with ILI pressure applied matches the ILI measured shape. Then the model geometry at zero pressure (referred to as the “depressurized shape”) will form an accurate starting point for calculating the pressure-stress relationship in the dent.
- Apply a range of pressures covering the operational pressure history and extract the resulting stresses for the fatigue life calculation.
Value
TDW integrity engineer help operators gain insights into large dent populations, complex dents and other real-world issues efficiently, enabling our customers to make data-driven decisions about their critical assets when it matters.
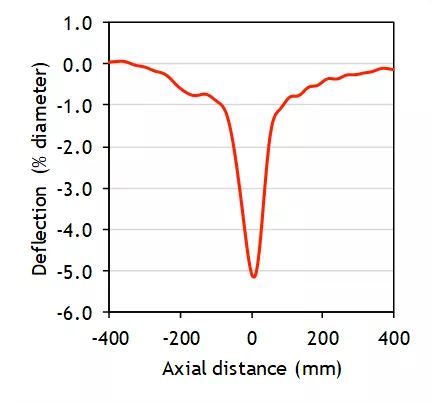