2
Article
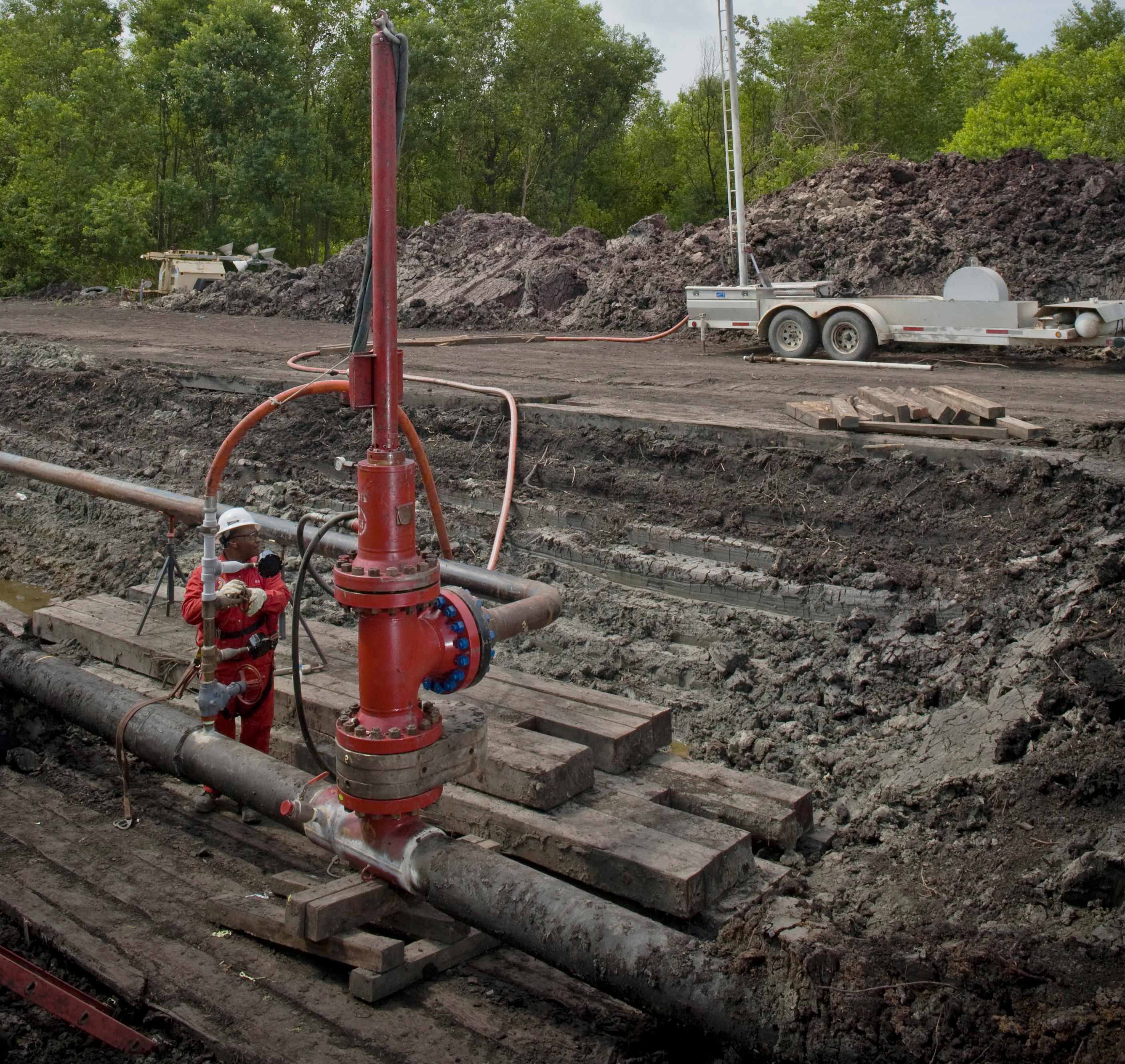
Pipeline Isolation: Essential Techniques and Best Practices
by Aaron Madden, Senior Product Manager, TDW
Pipeline isolation creates a safe work zone for personnel to perform maintenance, modification or repair without the risk of product exposure. By isolating a specific section of the pipeline, operators can safely access and work on the pipeline without endangering crews, assets or the environment. It’s an essential part of pipeline operations.
There are multiple ways to temporarily isolate a pipeline section. Choosing the most suitable approach depends on a number of variables, including why the isolation is necessary (performing maintenance on a specific pipeline section may call for a different solution than connecting a new pipeline to an existing system); operating conditions, including pressure, temperature and flow rate; pipeline size; risk assessment; and safety or regulatory requirements.
On or Off?
Another key consideration is whether the operator wants the system to remain in service while the work is being performed. Keeping a pipeline in service can be achieved with a bypass that allows product to continue flowing around the work area.
Some forms of isolation, including the use of blind flanges, require the entire system to be blown down (or purged) and the contents released into a safe location. Assuming the valves on the network are perfectly tight, shutdown and purging is an option but it has serious drawbacks: loss of product and sales, service interruptions and a potentially large volume of methane emissions, not to mention the high costs associated with decommissioning and depressurization.
There are three isolation (or line stopping) techniques that avoid those issues. Single block, double block and bleed (DBB) and double block and monitor (DBM) isolations are done while the system remains pressurized and, in some cases, production continues through a bypass. This bypass allows a section of the pipeline to be isolated while still enabling product flow around the work area and through the rest of the pipeline. Because of their advantages, including reduced downtime, increased safety and improved efficiency, these techniques have become the primary isolation methods used today.
- Single block isolation is the simplest of the three. It involves using a single block tool to isolate the section. TDW STOPPLE® plugging machines have represented the safest and most reliable solutions for single block isolations since 1953. They are made for pipelines 2 inches up to 56 inches with operating pressures from 19 bar to 102 bar (285 psi to 1480 psi) and in some special cases up to 153 bar (2220 psi).
- DBB is generally considered the use of two plugs or seals to isolate a section, with a bleed valve to release pressure between the seals. In most cases the bleed valve is monitored to ensure that both plugging heads are effectively sealing. The STOPPLE Train DBB system allows two plugging heads to be inserted into a line through a single fitting. This unique, patented design cuts fitting costs in half and reduces in-service welding time. The STOPPLE Train system provides a double block seal for pipelines from 4 inches to 36 inches at pressures up to 102 bar (1480 psi).
- DBM isolation also involves using plugging heads to create a physical barrier on both sides of the isolated section, but it differs from DBB because of an integrated monitoring device that continuously verifies the annulus pressure and the integrity of the seal. A rise in pressure can indicates a leak in one of the seals, or could be as innocuous as fluid expansion due to increased daytime temperatures. The remote-controlled TDW SmartPlug® system, which is primarily used in offshore isolations, provides DBM assurance for 8-inch through 48-inch pipelines, sealing against up to 350 bar (5,075 psi) operating pressure.
In addition, isolation can be performed using mechanical joints (particularly on smaller diameter pipelines); ball valves (a rotating ball with a hole through it to control the flow of fluid, used for low-pressure, low-temperature applications); and gate valves, which use a wedge-shaped gate to control the flow of fluid.
An illustration of a double block and bleed isolation with a bypass that allows production to continue around the work zone.
Deploying the Technology
Isolation technology accesses the pipeline through either non-intrusive or intrusive means. Non-intrusive methods do not require physically penetrating the pipeline wall, while intrusive techniques do.
The TDW SmartPlug® isolation tool is non-intrusive; it is pigged from the launcher to the set point then recovered at the receiver after the isolation operation has been completed. By contrast, the vast majority of DBB technologies are considered intrusive; they are deployed through a fitting welded onto the pipeline following a hot tap — a precise operation where a hole is cut in a live pipe.
In-service (or live line) pipeline welding is a specialized technique that has been used routinely and safely for decades. It can significantly reduce downtime and costs, but ensuring the weld quality, which is essential to pipeline integrity, is critical. In-service welding is performed by highly trained and experienced personnel. The procedure is subject to local and federal regulations, including API 1104, API 1107, ASME Section IX, BS4515, BS6990, and CSA Z662. In many cases, third-party inspections are required to verify the quality of the weld and compliance with regulations.
TDW has played a significant role in the advancement of hot tapping and plugging (HT&P) technology, including introducing the industry’s first high-pressure tapping machine nearly 75 years ago. The latest generation of TDW tapping machines are pressure balanced and hydraulically operated to provide greater safety and ease of use, with a variable feed and speed feature for greater control. Remote-controlled tapping operations for extreme environments reduce project and schedule risk even more.
A video that showcases how a STOPPLE® Train isolation works.
New Technologies, New Challenges
Isolation is a critical aspect of pipeline operations, ensuring safety and preventing product loss and emissions.
Before any isolation, operators and service providers should:
- Conduct a thorough risk assessment to identify potential hazards and develop appropriate mitigation measures.
- Establish clear and detailed procedures for isolating pipelines, including the use of isolation technologies, verification methods and emergency response plans.
- Develop and regularly practice emergency response plans to address potential incidents, such as leaks or fires.
- Ensure that every person involved in pipeline isolation is trained and qualified to perform their duties safely and effectively.
Isolation techniques can be used on pipelines carrying any type of product, from crude oil, refined products and natural gas to petrochemicals and liquefied natural gas (LNG). Single block, DBB and DBM technology all provide a robust and reliable seal, but as pipelines begin to carry new products such as hydrogen, ensuring a “leak tight” seal will become even more critical. This requires the use of high-quality isolation devices, regular inspections and maintenance, and strict adherence to safety protocols and relevant regulations. The American Petroleum Institute (API) provides several standards that address pipeline isolation techniques, including DBB and DBM. Key regulations include API 1104, a comprehensive standard covering various aspects of pipeline design and construction, including isolation devices. API 1104 specifies requirements for the selection, installation, and testing of isolation devices, such as valves and fittings. In addition, API provides detailed specifications for valves used in oil and gas pipelines, including outlining performance requirements, testing methods and inspection procedures for isolation valves.
TDW strictly adheres to industry regulations and standards to ensure our isolation systems are designed, installed and maintained in accordance with industry best practices. This commitment to excellence enhances safety, boosts reliability, and helps operators reduce downtime and associated costs.