2
Case Study
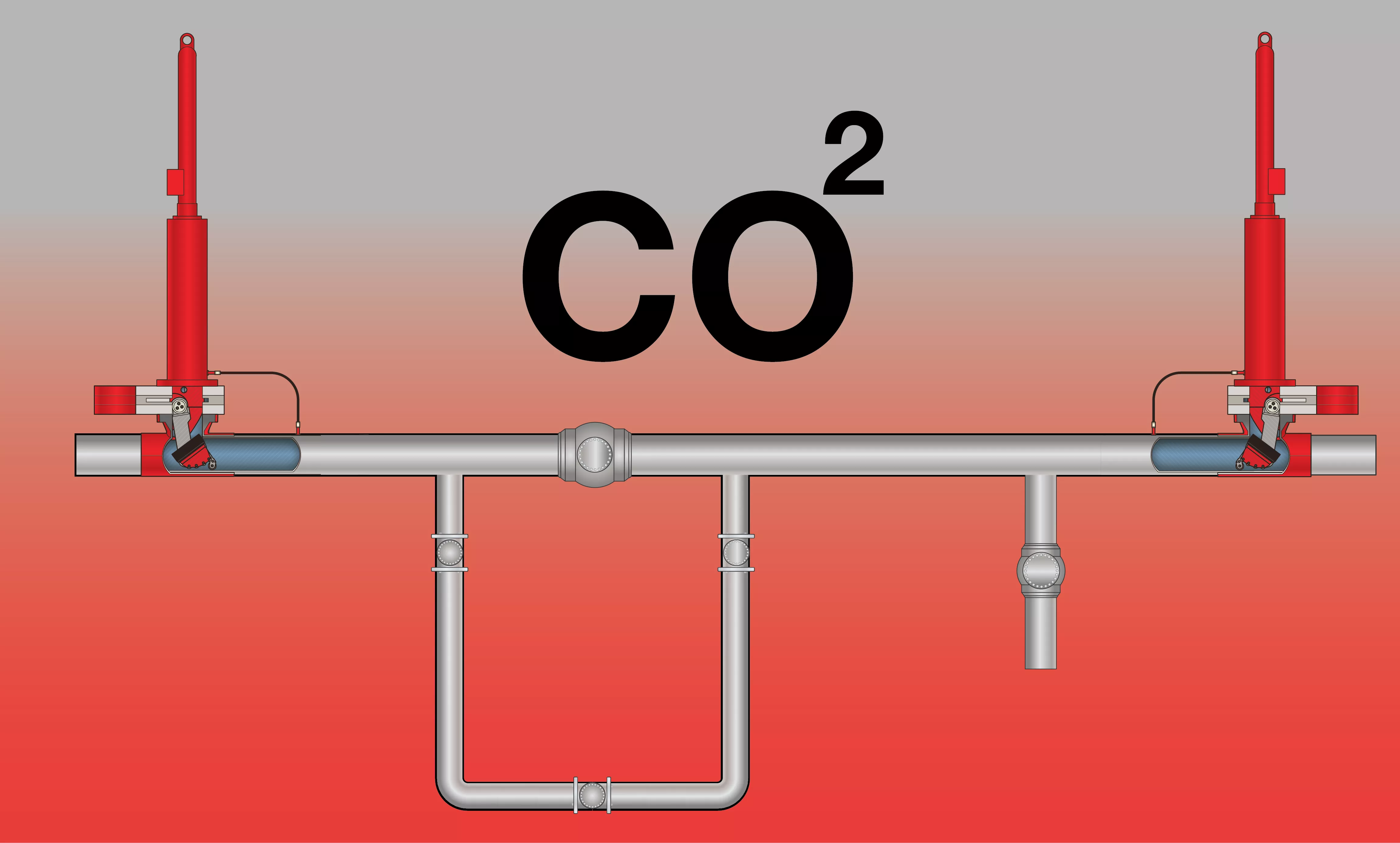
Innovative Solutions for Pipeline Intervention and Isolation in Carbon Dioxide (CO₂) Transport
TDW Offering: Intervention and Isolation - High Pressure
Technology: In-Service Welding, STOPPLE®, LOCK-O-RING®
Project Location: United States of America
Keeping the Pipeline Flowing
Pipeline operators require the ability to modify, repair, and swiftly address emergency situations. Within their arsenal of solutions, hot tapping and plugging techniques stand out as indispensable tools. The intervention process commences with the installation of a STOPPLE® split tee with appropriate in-service welding and non-destructive testing procedures. A hot tapping operation is then executed using a temporary sandwich valve to extract the coupon and create a point of entry into the pipeline. An isolation tool is then deployed to isolate the section of the pipeline, and when necessary, a bypass can be installed to maintain uninterrupted flow
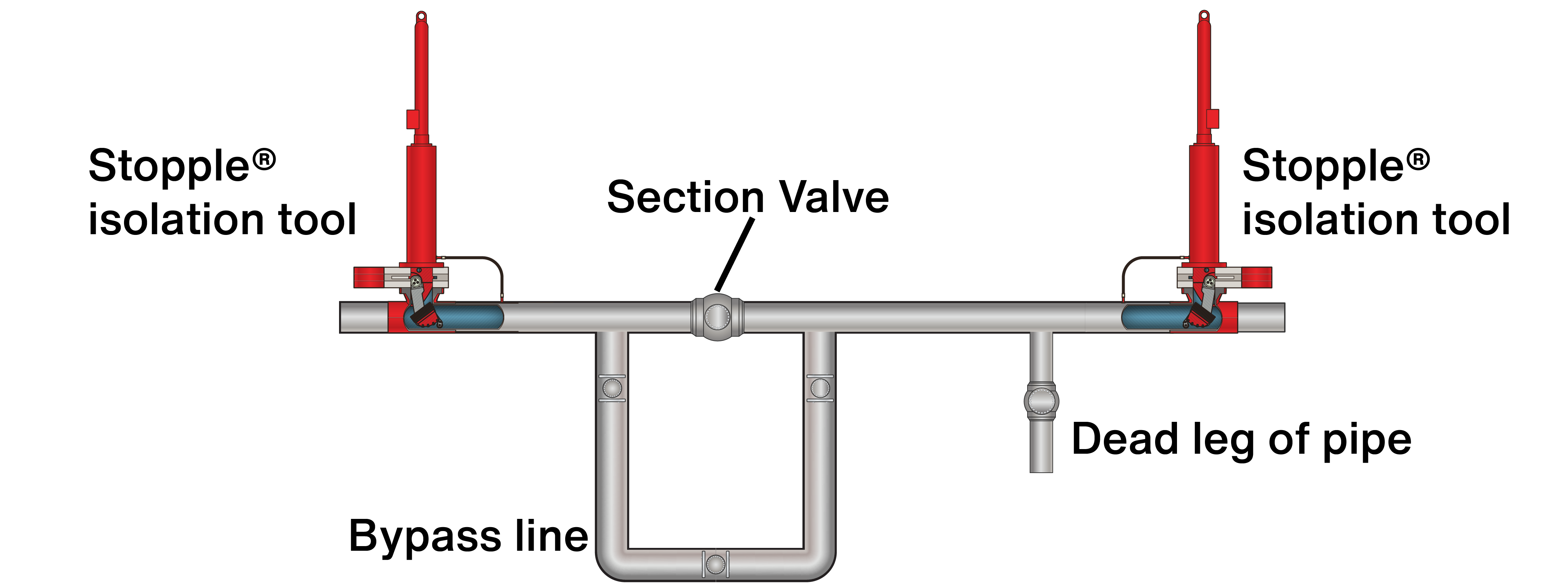
Diagram of the double STOPPLE® isolation.
Pipeline Operator's Challenge
During a routine pipeline cleaning, the operator encountered a series of challenges. Firstly, one of the cleaning pigs became lodged within the pipeline and needed to be removed. Simultaneously, they uncovered a nearby section valve that was leaking, which needed to be replaced. Crucially, the operator was determined to resolve these issues without disrupting the pipeline's continuous operation. The pipeline has been in operation for over 20 years and has undergone numerous cleaning and inspection cycles. It primarily transports liquid-phase Carbon Dioxide at a substantial pressure of up to 2400 psi (165 bar), making it essential to maintain a minimum pressure of 2000 psi (138 bar) during the intervention.
Accomplishing a hot tap and isolation at such elevated pressure levels demands specialized equipment. Furthermore, the transported product contains around 1% H2S, which necessitates extra precautions due to the gas's toxicity and the corrosive environment it can induce.
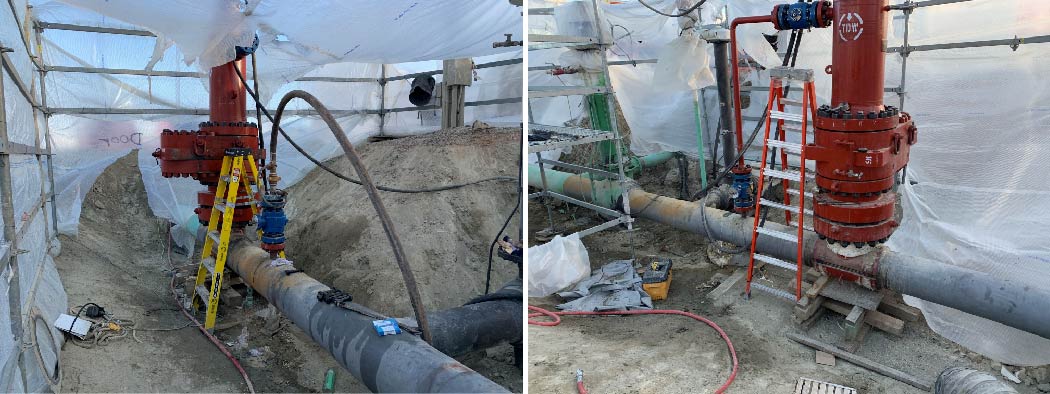
Two STOPPLE® tools are deployed, successfully isolating the affected section of the pipeline.
TDW Solution
Our longstanding partnership with the customer commenced many years ago. Notably, in 2005, TDW custom-designed equipment to cater to the unique requirements of the customer. This specialized equipment package includes SANDWICH® valves with a class 900lbs rating, as well as STOPPLE® heads designed to withstand pressures of up to 2200 psi. Moreover, spools were fabricated to seamlessly interface with the STOPPLE® split tee rated at 1500lbs. These equipment components have proven their reliability and effectiveness since their inaugural use in 2006.
However, it's not just the cutting-edge equipment that contributes to our success; it's also the wealth of experience accumulated over the past two decades of working with these products. Our seasoned engineers take into consideration a spectrum of critical factors, including rapid gas decompression, Hydrogen embrittlement, cooling effects during in-service welding and the safe management of product bleeding from the equipment. These aspects are meticulously addressed in the work methodology to ensure the successful execution of each project.
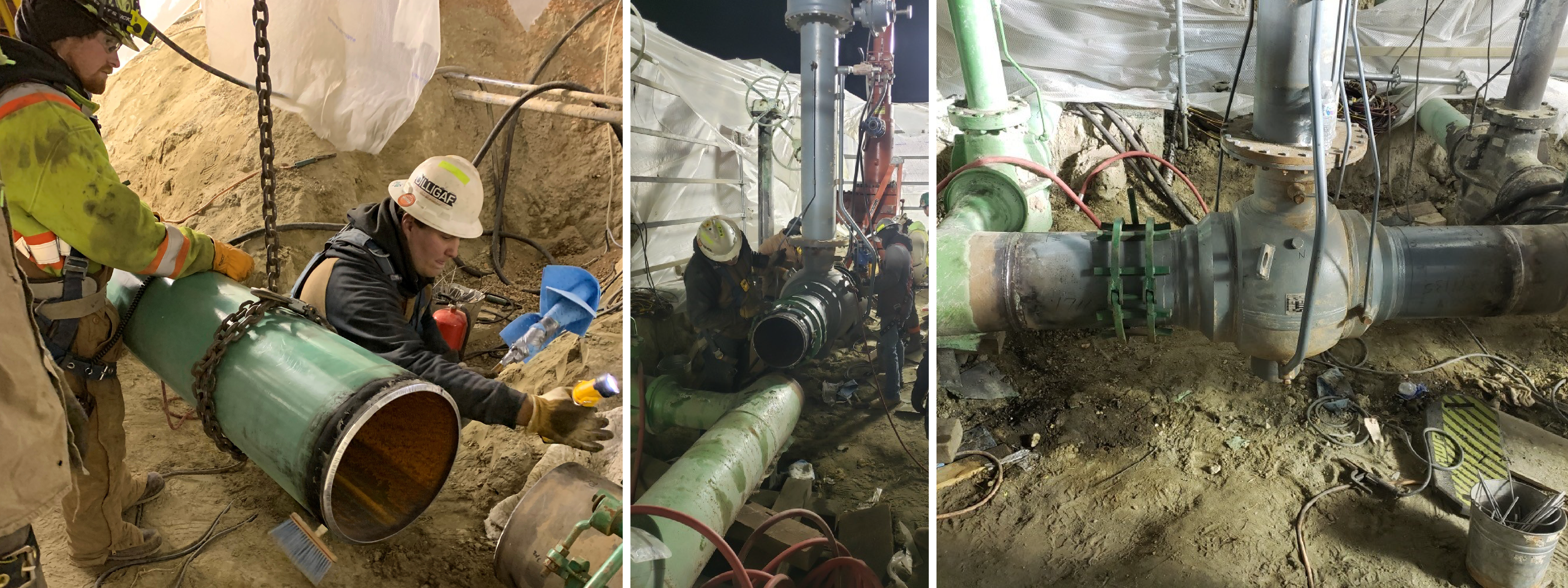
Repairs and maintenance are completed on the pipeline. The leaking section valve is replaced with a new valve.
Outcome
The deployment of the SANDWICH® valves and STOPPLE® heads, built to withstand extreme pressures, exemplified our ability to adapt to the customer’s specific needs. Using these custom-designed tools we were able to successfully complete a hot tap and isolation of the affected section of the pipeline while maintaining minimum pressure levels of 2000 psi. After the double STOPPLE® was set, the stuck pig was removed and the leaking section valve was replaced.
Throughout this endeavor, we solidified our customer relationship by delivering a solution that met their requirements and exceeded their expectations.
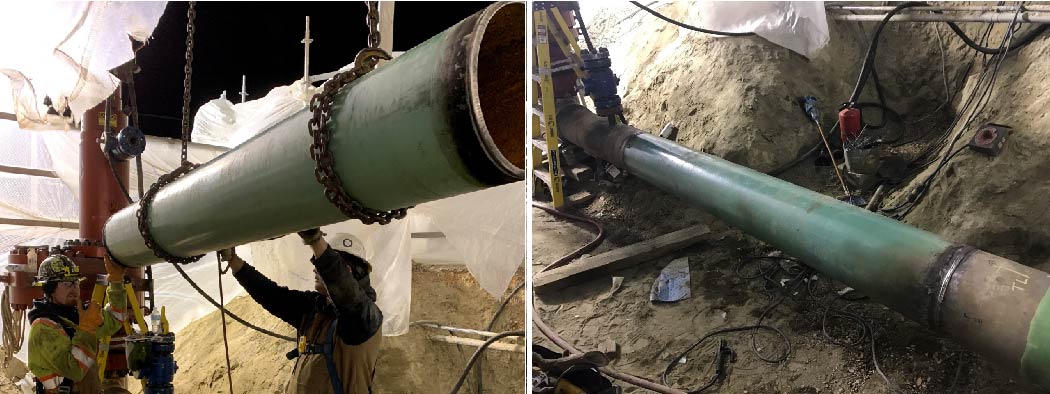
The inline tee and dead leg are removed and replaced by a straight section of pipeline.