Case Study
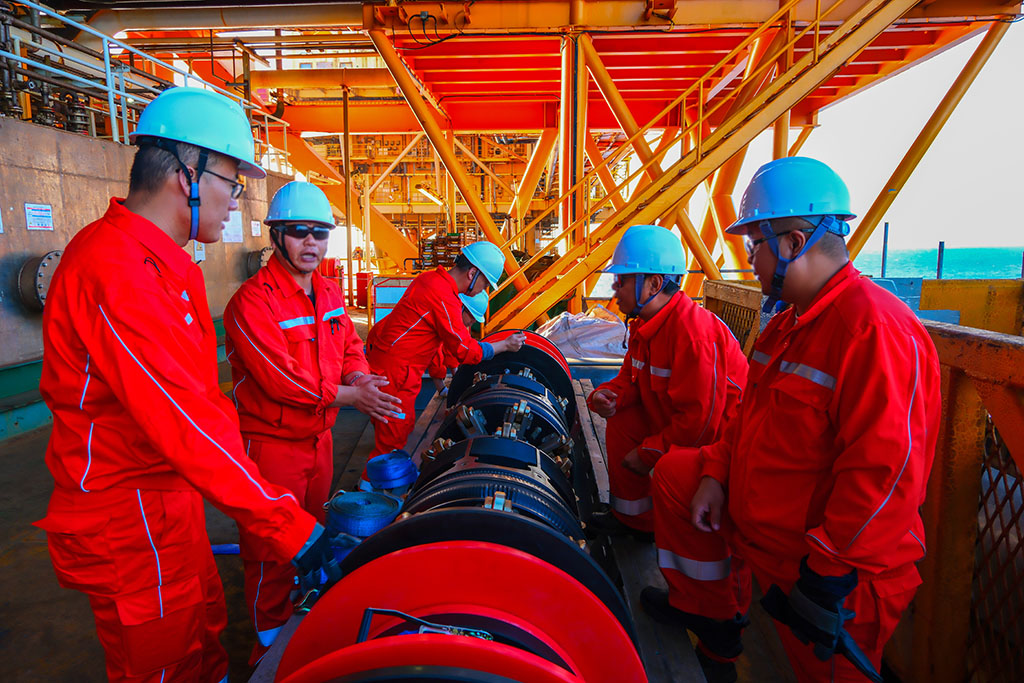
Unique Pipeline Isolation Application During Platform Upgrade in the East China Sea
TDW Offering: Non-Intrusive Isolation
Technology: SmartPlug®
Project Location: East China Sea
Offshore Isolations
Offshore pipeline isolation involves temporarily blocking a section of the pipeline so that maintenance, repairs or modifications can be performed safely without having to remove the pipeline content or shutting down production for a longer period. The isolation process can be challenging in an offshore environment due to several factors including variable weather and harsh sea conditions, accessibility or with operation taking place partly subsea.
In the case study below, the isolation solution and the technical expertise of TDW provided multimillion-dollar savings in potential lost production while maintaining safe isolation for more than 80 days to facilitate modification work at the offshore platform. The method involved the deployment of a Dual Module SmartPlug® isolation tool with gas production diverted through a bypass line on the gas export riser during the construction period.
Pipeline Operator's Challenge
A TDW client, China National Offshore Oil Corporation (CNOOC), had raised a requirement for isolations to facilitate the topside modification work at an offshore platform in the East China Sea. The client was planning for sectional replacement of the riser of the 28-inch Gas Export Pipeline (GEP) and installation of new pipework, valves, etc. topside between the pig launcher and the riser. To facilitate the safe execution of these works the client required temporary pressure isolation of the 28-inch GEP for 80 days. Since the pipeline plays a critical role in supplying gas to the mainline, construction had to be carried out continuously without interruption to gas production. Traditional hot-tapping and Stopple® isolation solutions were considered but were deemed impractical in the challenging settings of the project. One such challenge was isolating at a vertical position at the riser near the seawater level which would feature tight spaces and resource-intensive construction methods.
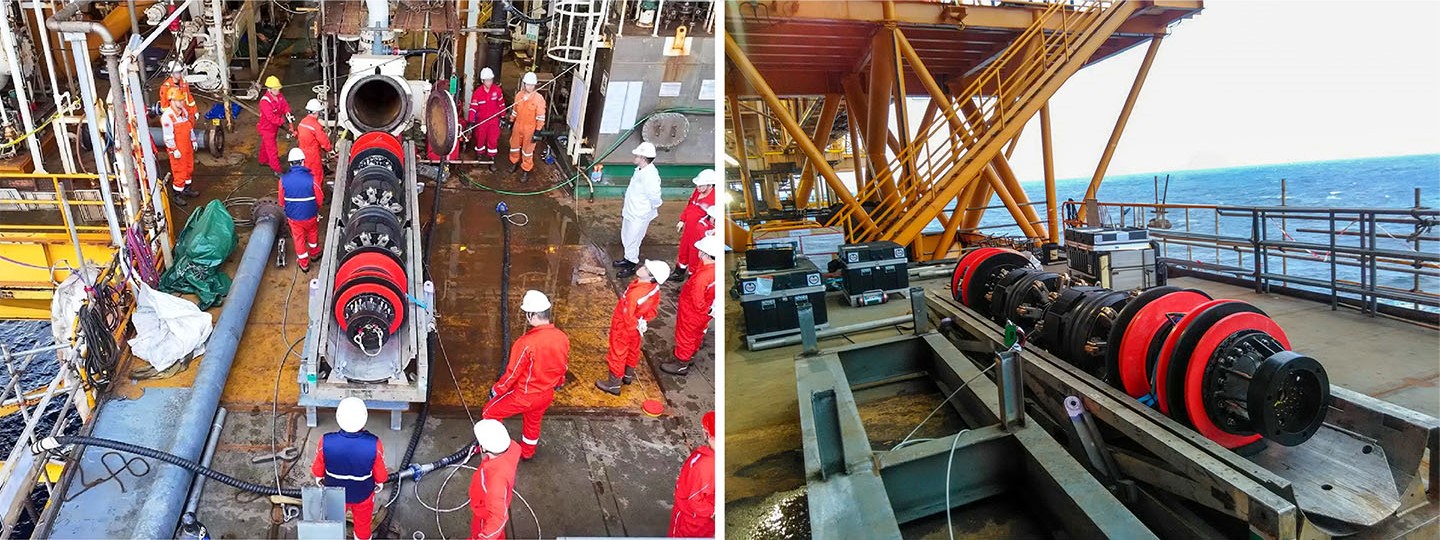
The TDW SmartPlug® tool being loaded into the customer pig launcher.
TDW Solution
For this project, TDW deployed a 28-inch Dual Module SmartPlug® tool to create double-block and monitor (DBM) isolation against the gas pressure in the pipeline. The DNV Type Approved SmartPlug® tool is remote-controlled by the SmartTrack™ communication system, which is used to monitor and track the SmartPlug® tool during the operation. For this project, one SmartPlug® tool had to complete two pipeline isolations during a single launching.
1. For the initial isolation the SmartPlug® tool was loaded and launched from the pig launcher on the offshore platform. It was then pigged through the topside components, past the ESDV valve and isolation joint, to the set location in the riser, a pigging distance of approximately 30 meters. Pigging pumping provided by the client services used N2. When the SmartPlug® tool was activated and set at the designated location, the piping upstream of the tool was depressurized to atmospheric to allow the riser to be cut and a new spool with a bypass tee installed.
2. In the second isolation, the SmartPlug® tool was repositioned a short distance to the top of the newly installed spool to isolate the pipeline to allow topside maintenance work. To do this the pressure across the SmartPlug® tool was equalized, the SmartPlug® tool was then unset and pigged to the second position by bleeding off the pressure above the isolation tool slightly. The bypass pipeline was connected from the topside to the newly installed tee and production opened. The pipeline was then isolated for the duration of the topside modification work, which took 70 days to complete.
Upon completion of all maintenance on the topside, the pressure across the SmartPlug® tool was equalized and unset, then pigged back to the launcher using gas pressure from the pipeline before being retrieved from the launcher, completing the isolation scope.
Customer pig launcher with SmartPlug® tool (left), SmartPlug® tool set at first isolation point (center)
and SmartPlug® tool set at the second isolation point (right).
Outcome
The project team completed the project well within the allocated time frame, managing the schedule seamlessly. This efficiency became more evident when the bypass line was installed, and the SmartPlug® tool was repositioned to the second isolation point. This strategic move allowed the client to continue producing and exporting gas from the platform, while modification work proceeded for an additional 70 days. This approach resulted in significant savings for the client, compared to the alternative of leaving the SmartPlug® tool at the first isolation location for the entire duration of the project. Moreover, the project boasted an impeccable safety record, with no health, safety and environmental (HSE) incidents occurring. The successful execution of both isolations further underscores the expertise and precision that customers can expect when partnering with TDW.
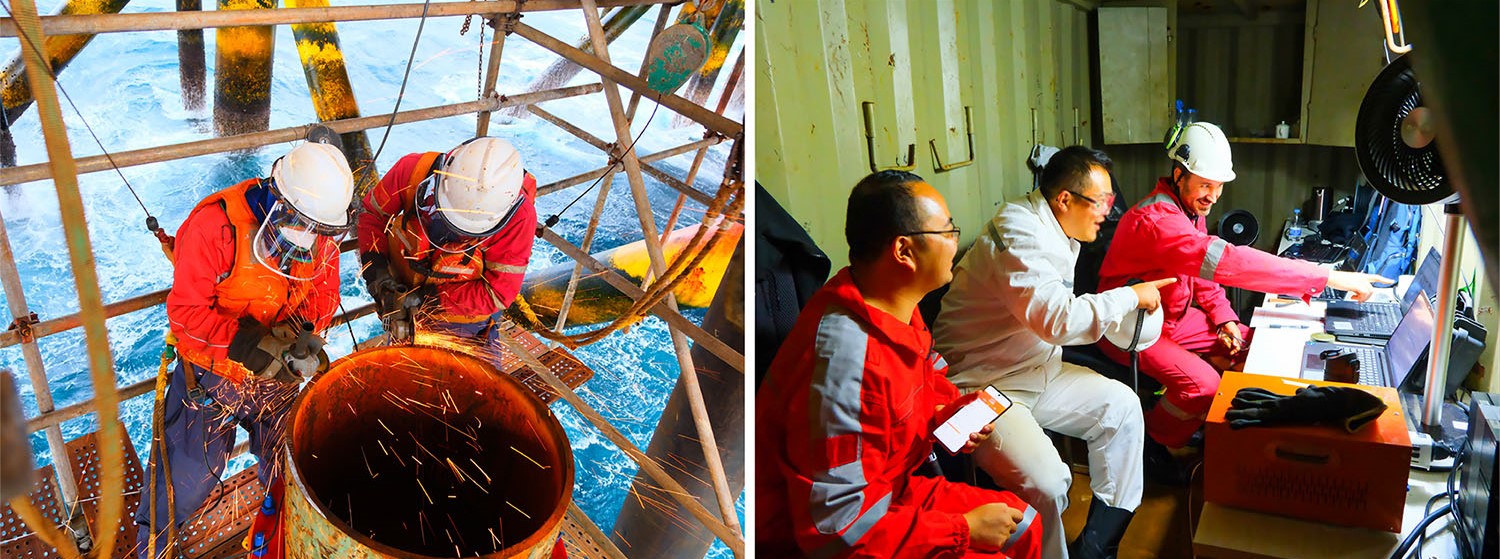
Repairs and maintenance are completed on the pipeline thanks to a secure Smartplug® isolation (left).
A TDW technician showcases the double-block and monitor (DBM) isolation that the Smartplug® tool achieved (right).