SpirALL® Electromagnetic Acoustic Transducer (EMAT)
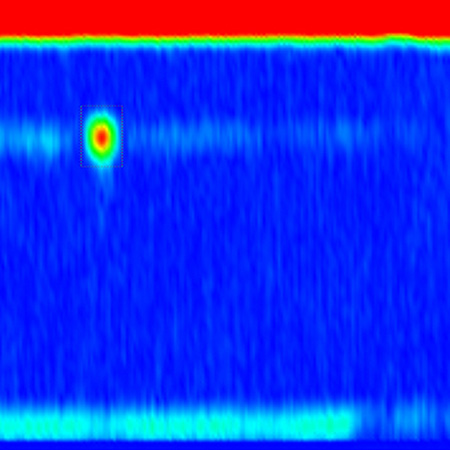
Designed to enhance in-line inspection and give pipeline owners and operators more confidence about inspection results for crack detection, SpirALL® Electromagnetic Acoustic Transducer (EMAT) technology finds anomalies that magnetic flux leakage-based technology is unable to detect.
SpirALL EMAT technology can be used in either liquid or gas pipelines without requiring a couplant.
Combining SpirALL EMAT data with data produced by the various technologies on the MDS™ (Multiple Datasets) platform enables more accurate characterization of pipeline defects.
Key Features
- Innovative design produced redundant data across multiple channels to reduce the likelihood of false or irrelevant data being erroneously recorded as a defect
- Data correlation with MDS eliminates false calls for non-critical features and delivers all pipeline features and anomalies in a single report
Sizes
- 10-inch through 16-inch
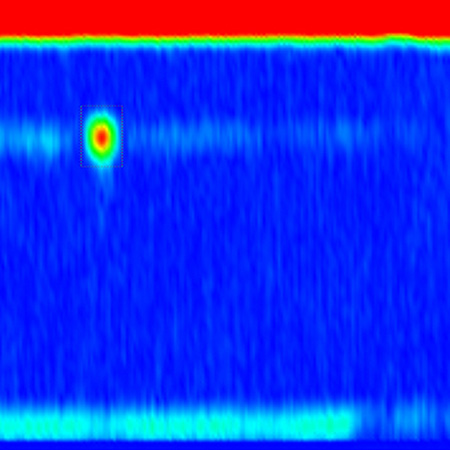
Designed to enhance in-line inspection and give pipeline owners and operators more confidence about inspection results for crack detection, SpirALL® Electromagnetic Acoustic Transducer (EMAT) technology finds anomalies that magnetic flux leakage-based technology is unable to detect.
SpirALL EMAT technology can be used in either liquid or gas pipelines without requiring a couplant.
Combining SpirALL EMAT data with data produced by the various technologies on the MDS™ (Multiple Datasets) platform enables more accurate characterization of pipeline defects.
Key Features
- Innovative design produced redundant data across multiple channels to reduce the likelihood of false or irrelevant data being erroneously recorded as a defect
- Data correlation with MDS eliminates false calls for non-critical features and delivers all pipeline features and anomalies in a single report
Sizes
- 10-inch through 16-inch