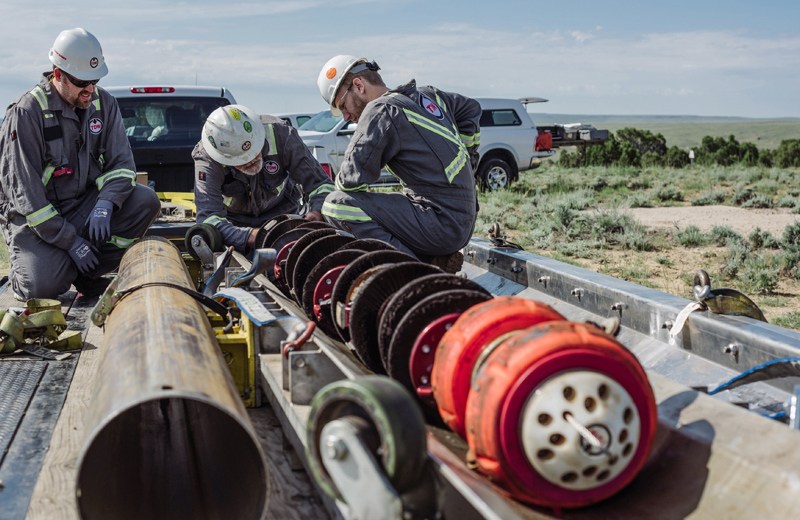
Comprehensive Threat Assessment
Regardless of their cause, undetected or mischaracterized pipeline defects are a threat to operations, asset life, the environment and public safety. By providing end-to-end integrity solutions — from assurance-based cleaning to actionable inspection results — TDW helps you meet your risk reduction goals, optimize integrity actions and comply with regulations.
TDW integrity engineers know which in-line inspection (ILI) and non-destructive evaluation (NDE) technology is most suitable for detecting, characterizing and verifying defects in your pipeline. Our comprehensive solution includes technology to assess individual and interacting threats, including Stress Corrosion Cracking (SCC) and Selective Seam Weld Corrosion (SSWS). Because ILI is performed while pipeline product is flowing —unlike hydrotesting, which is disruptive and requires the system to be depressurized first — there are no harmful emissions released into the atmosphere.