XYZ Mapping
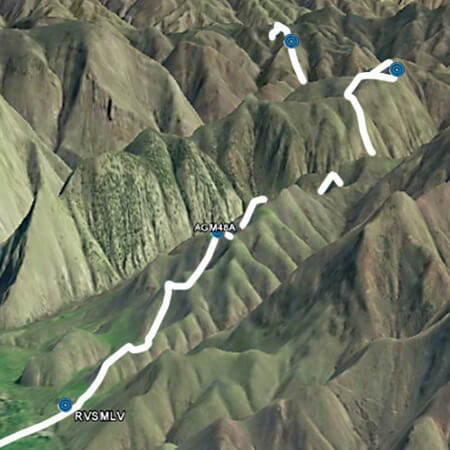
High resolution XYZ mapping technology from TDW pairs global positioning system (GPS) coordinates at above-ground locations with inertial mapping. The result: highly accurate coordinates for all reported features, including valves, fittings and anomalies. If you need to conduct an excavation, the system will guide you to the right spot, eliminating the time and expense of “walking the pipeline.”
Key Features
- Provides sub-meter GPS coordinates for an entire pipeline
- Measures pipe centerline latitude, longitude and elevation
- Enables bending strain analysis
- Allows you to monitor pipeline displacement
Sizes
- 6-inch through 48-inch
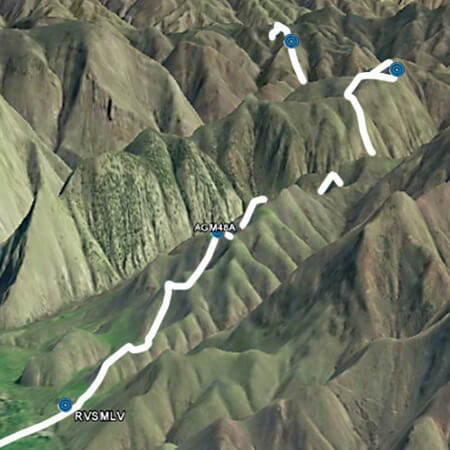
High resolution XYZ mapping technology from TDW pairs global positioning system (GPS) coordinates at above-ground locations with inertial mapping. The result: highly accurate coordinates for all reported features, including valves, fittings and anomalies. If you need to conduct an excavation, the system will guide you to the right spot, eliminating the time and expense of “walking the pipeline.”
Key Features
- Provides sub-meter GPS coordinates for an entire pipeline
- Measures pipe centerline latitude, longitude and elevation
- Enables bending strain analysis
- Allows you to monitor pipeline displacement
Sizes
- 6-inch through 48-inch