SpirALL® Magnetic Flux Leakage (SMFL)
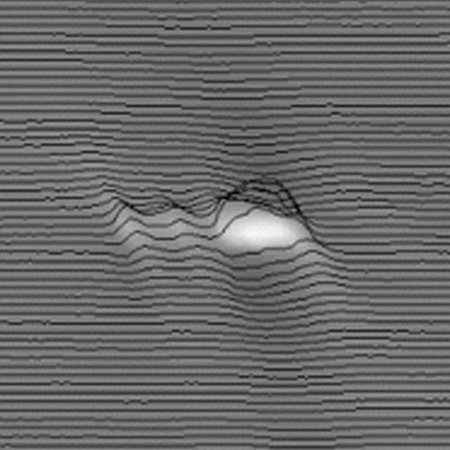
Proven over thousands of kilometers of pipeline, SpirALL® magnetic flux leakage (SMFL) technology overcomes the limitations of axial high-resolution magnetic flux leakage (MFL) alone in characterizing axially oriented defects in the pipe wall and long seams. With SpirALL® magnetic flux leakage (SMFL) technology, pipeline owners and operators have an efficient way to detect crack-like defects in the pipe wall and long seams — including selective seam weld corrosion, hook cracks, lack of fusion, and surface-breaking laminations.
SpirALL MFL is combined with other technologies on the Multiple Dataset (MDS) platform to provide comprehensive threat assessment in a single inspection run.
Key Features
- Compact magnetizer design to create a spiral or transverse magnetic field that provides 100% coverage of the pipe wall
- Detects axial planar or crack-like defects not detected by axial MFL
- Able to distinguish attributes of long seam type — electric resistance welded (ERW), electric fusion welded (EFW), double submerged arc welded (DSAW), lap welded
Sizes
- 6-inch through 30-inch*
* not available in some diameters
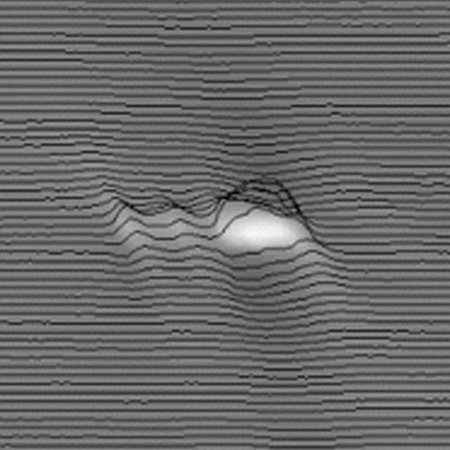
Proven over thousands of kilometers of pipeline, SpirALL® magnetic flux leakage (SMFL) technology overcomes the limitations of axial high-resolution magnetic flux leakage (MFL) alone in characterizing axially oriented defects in the pipe wall and long seams. With SpirALL® magnetic flux leakage (SMFL) technology, pipeline owners and operators have an efficient way to detect crack-like defects in the pipe wall and long seams — including selective seam weld corrosion, hook cracks, lack of fusion, and surface-breaking laminations.
SpirALL MFL is combined with other technologies on the Multiple Dataset (MDS) platform to provide comprehensive threat assessment in a single inspection run.
Key Features
- Compact magnetizer design to create a spiral or transverse magnetic field that provides 100% coverage of the pipe wall
- Detects axial planar or crack-like defects not detected by axial MFL
- Able to distinguish attributes of long seam type — electric resistance welded (ERW), electric fusion welded (EFW), double submerged arc welded (DSAW), lap welded
Sizes
- 6-inch through 30-inch*
* not available in some diameters